Recently the Haulotte Pre-Delivery (PDI) team switched to a new electronic program for managing their jobs on different machines.
Using a Samsung tablet and specially adapted software ‘Destiny’, technicians can now record the information related to the machine being worked on, including machine details, all checks and quality assurance, and time worked. This is all linked to other internal Haulotte data, making for seamless recording and tracking.
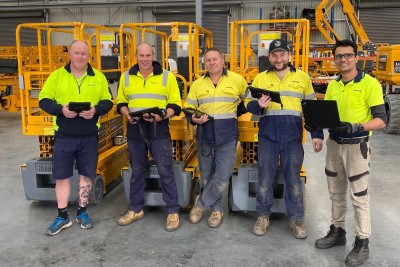
To be more productive on other machines
Evan Goulis Operations Manager for Haulotte.
Evan